Robust and reproducible non-lithographic patterning of three-dimensional (3D) metal micro-structures metallic micro/nanostructures has attracted extensive research attentions for the great potential applications in the design of microelectronics, micro sensors, microelectromechanical systems (MEMS), microfluidics and analysis devices. Most of the traditional additive manufacturing technologies are applicable for fabrication of true 3D micro components/assemblies. However, the need of advanced facilities, expensive materials and the limited resolution (approximately no better than 50 µm) have limited the wide application of such complex structures.
In a recent study published in Nanoscale (2017, doi: 10.1039/c7nr03803h)(http://pubs.rsc.org/en/content/articlelanding/2017/nr/c7nr03803h), a dynamic electromechanical resonance technique for the characterization of mechanical properties of the 3D helical structures is reported by researchers from Ningbo Institute of Materials Technology and Engineering. Along with the previously reported static pull-in method in Microsystems & Nanoengineering (2016, doi: 10.1038/micronano.2016.10)(https://www.nature.com/articles/micronano201610), the mechanical properties of both the 3D structures and the materials can be analyzed by the probe-based dynamic or electrostatic techniques.
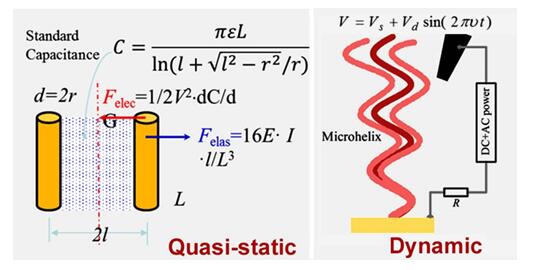
Figure 1. A probe-based mechanical testing methods for 3D complex structures.
A procedure that directly writes ultralow flexural helical metallic micro/nanostructures onto device surfaces is alsodemonstrated by a novel meniscus-confined electrodeposition (MCED) from a computer-controlled micropipette for the first time. The authors found that the centersymmetric and vertical double copper microhelix structure with 1.2 μm wire diameter has a flexural rigidity of 0.9 × 10−14 N•m2 and a superior electrical conductivity of 2785 S•cm−1. This convenient and robust fabrication method may find applications in liquid flow rate sensors and chemical-stimulated actuators with ultrahigh sensitivity.
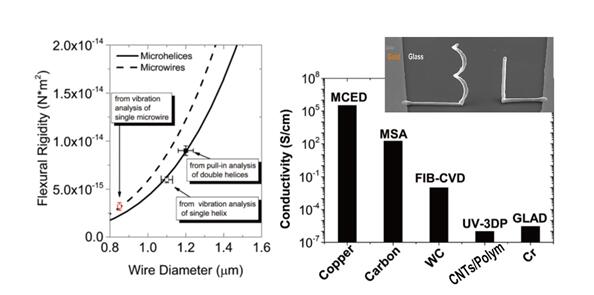
Figure 2. Ultrahigh flexural rigidity and conductivity of copper microhelix fabricated by a novel MCED technology
This study was supported by the National Natural Science Foundation of China (No. 11574331 & 11674335) and the Ningbo Science & Technology Bureau (No. 2016B10005 & 2015B11002).
Associate Professor Jianjun Guo: jjguo@nimte.ac.cn